Running a delivery operation is expensive. But for companies who utilize electronic Proof of Delivery (ePOD), the benefits add up pretty quickly. We’re talking eliminating- or at least easily resolving- payment disputes, decreasing labor and fuel costs, improving margins (thru better inventory control), reducing driver turnover (because they have the right tools to do their jobs), and most of all – improved customer satisfaction yielding long-term loyalty.
For most delivery-distribution companies who want to implement and automate ePOD effectively, it is important to understand the steps that go into it.
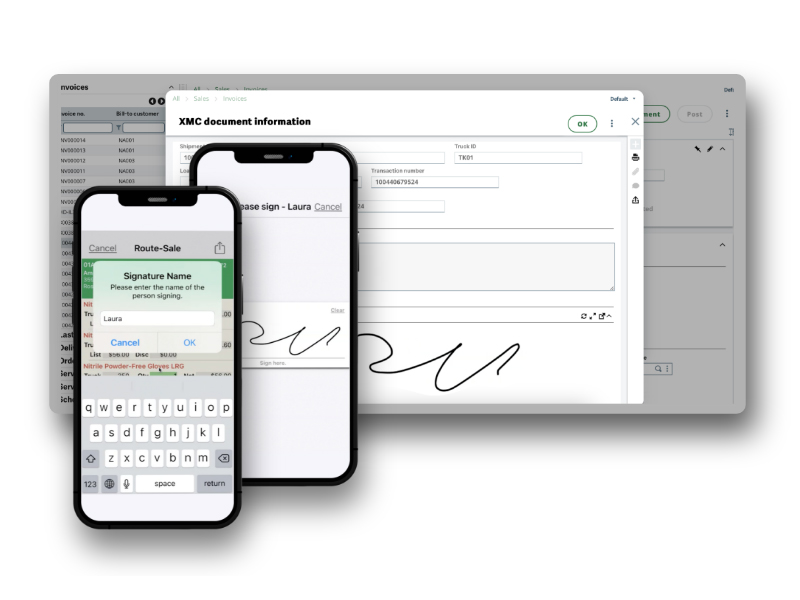
1. Route Planning.
There should be careful consideration and analysis before sending drivers out on the road. After all, the goal is for drivers to make as many successful deliveries as possible, in the shortest amount of time, while consuming the least amount of fuel. Do drivers visit the same customers on a regular basis, or are the delivery routes different each day? Does the customer have any special receiving hours? What about the vehicles – do they all have the same capacity? Are there temperature control issues?
2. Picking.
Once your route plans are set, the next major consideration is assigning the products to the trucks. Are you picking by order? Are there pallets or other containers that also must be picked? What is the timing? If warehouse personnel are picking, they often pick to a staging area the night before. However, if drivers are picking, they may pick straight onto the truck.
3. Truck Loading.
After picking, the next major process is truck loading. First in, last out is a good rule of thumb. In some situations, the driver is also expected to "backhaul” goods. These are goods picked up and transported back to the warehouse. For example, the goods might be customer returns or material from suppliers. In those situations, it’s important to have somewhere in the truck to place picked up goods.
4. Mobile App for the Driver.
To be successful, a driver should have everything they need, at their fingertips, to ensure accurate and speedy delivery. This includes the ability to see the planned order of delivery stops, integration with the device map for turn-by-turn directions. This may include easy access to memos, documents, surveys, reports or other intelligence to optimize each customer visit.
5. Gathering Critical Information.
What information should your drivers collect? First off, they should be able to record any changes to the delivery order, such as the quantity delivered. They also may wish to capture the name of the person signing, the signature itself, as well as a photo, or photos. Ideally, the mobile app should also record geo coordinates and a date and time stamp. In many cases, the driver may also wish to leave the customer with a printed proof of delivery document that includes all this critical information.
6. ERP integrated.
Your ePOD software solution will be much more effective if it integrates with your ERP, allowing you to leverage ERP’s data with the critical information gathered as part of the ePOD process.
If you would like to learn more about integrating electronic Proof of Delivery to your Acumatica or Sage ERP system, contact xkzero.